The Ultimate Overview to Fillet Weld Quality Assurance: Guaranteeing Strength and Durability in Your Welded Joints
In the realm of welding, making certain the stamina and toughness of fillet welds is extremely important for the honesty of bonded joints. The quality assurance measures implemented during the welding procedure can substantially affect the structural soundness of the end product. From the option of suitable products to the careful inspection of welds, each step plays a critical function in establishing the general high quality of the weld joint. As we begin on this exploration of fillet weld quality assurance, we will certainly reveal essential factors that influence weld strength, look into efficient inspection approaches, and go over techniques for avoiding common weld issues. Stay tuned to find how mastering these methods can elevate the longevity and reliability of your bonded joints.
Significance of Fillet Weld High Quality Control
Guaranteeing proper fillet weld top quality control is extremely important in guaranteeing the architectural honesty and longevity of welded elements in various markets. Fillet welds are frequently used in architectural steelwork, bridges, pressure vessels, pipes, and other vital framework where the strength of the weld is essential to general safety and performance. Quality control measures such as aesthetic evaluations, non-destructive testing, and adherence to welding treatments aid identify possible problems like lack of combination, insufficient infiltration, undercutting, or excessive reinforcement.
Key Variables Impacting Weld Strength
Attaining optimum weld toughness needs cautious factor to consider of different essential elements that influence the stability and toughness of the bonded joint. The initial essential aspect is correct joint preparation, which involves cleansing the base steels to remove any contaminants that can compromise the weld. In addition, the fit-up of the joint is essential to make certain appropriate infiltration and blend of the filler material.
The selection of the ideal welding strategy and parameters additionally plays a considerable duty in figuring out weld strength. Aspects such as heat input, travel speed, and electrode angle can influence the high quality of the weld. Preserving the appropriate interpass temperature level throughout multi-pass welding is important to avoid splitting and make sure a solid bond between the layers.
In addition, the option of filler material and its compatibility with the base metals is important for accomplishing high weld toughness. Utilizing filler material with the appropriate mechanical residential or commercial properties can enhance the total integrity of the weld. Lastly, post-weld heat treatment and correct evaluation methods are necessary action in making certain the strength and toughness of the bonded joint.
Examination Methods for Weld Stability
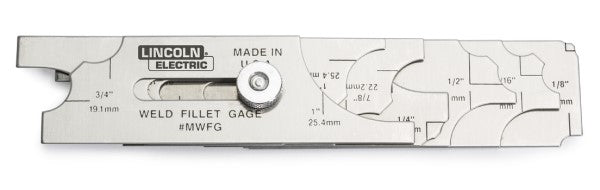
An additional critical examination technique is fluid penetrant testing, where a liquid dye is related to the weld surface - Gauge Fillet Weld. The dye seeps right into any surface-breaking defects, making them noticeable under UV light. This technique works for spotting imperfections that might not be noticeable to the nude eye


Ultrasonic testing is also widely made use of for inspecting weld honesty. High-frequency acoustic wave are guided into the weld, and any type of disturbances in the sound wave pattern suggest possible flaws like cracks or absence of fusion.
These assessment approaches play an essential role in making sure the quality and dependability of welds, inevitably adding to the total toughness and durability of bonded joints in industrial settings.
Avoiding Usual Weld Flaws
In order to maintain the structural honesty of welded joints in commercial applications, it is essential to implement precautionary measures to attend to typical weld this hyperlink defects. One typical flaw is lack of fusion, where the filler product fails to bond sufficiently with the base metals, causing weak places in the weld. This can be avoided by making certain correct warmth control and making use of the proper welding method.
Another frequent problem is porosity, brought on by gas entrapment useful site in the weld metal during the welding process. To avoid this, it is important to clean up the base metals extensively, use completely dry electrodes, and maintain a suitable welding environment with appropriate air flow.
Additionally, cracks in welds can jeopardize the joint's stamina. To avoid this problem, it is very important to control the air conditioning price after welding, utilize pre-heating when essential, and select suitable welding criteria.
Enhancing Weld Toughness With Correct Methods
One vital approach to improve weld longevity is to make sure appropriate weld grain positioning. By positioning the weld bead properly within the joint, the weld's strength and resistance to tiredness can be substantially boosted.
In addition, utilizing ideal pre-weld and post-weld warmth treatments can aid minimize recurring stresses and improve the weld's durability, making it a lot more resistant to cracking and failing with time. Another technique to improve weld sturdiness is to utilize premium welding consumables and base materials. Selecting the ideal filler metal and ensuring the cleanliness of the base steels can prevent incorporations and various other flaws that could jeopardize the weld's toughness. By executing these proper strategies, welders can make sure that their welded joints show outstanding stamina and resilience, meeting the best criteria.
Conclusion
To conclude, preserving premium quality control requirements for fillet welds is essential for guaranteeing the stamina and durability of welded joints. By recognizing the essential factors impacting weld strength, using inspection approaches for weld integrity, preventing usual weld defects, and employing correct methods, welders can enhance the overall longevity of their welds. It is crucial to prioritize quality assurance procedures to create resilient important site and trustworthy welded joints.
In the world of welding, ensuring the stamina and toughness of fillet welds is vital for the honesty of bonded joints. As we get started on this expedition of fillet weld top quality control, we will reveal crucial variables that influence weld toughness, dig right into effective assessment techniques, and go over strategies for protecting against typical weld problems.Achieving optimum weld toughness requires mindful factor to consider of numerous essential aspects that influence the stability and durability of the bonded joint (Gauge Fillet Weld).In verdict, preserving high top quality control standards for fillet welds is essential for ensuring the strength and sturdiness of bonded joints. By understanding the essential variables impacting weld toughness, utilizing evaluation methods for weld stability, avoiding usual weld problems, and utilizing proper strategies, welders can boost the overall durability of their welds